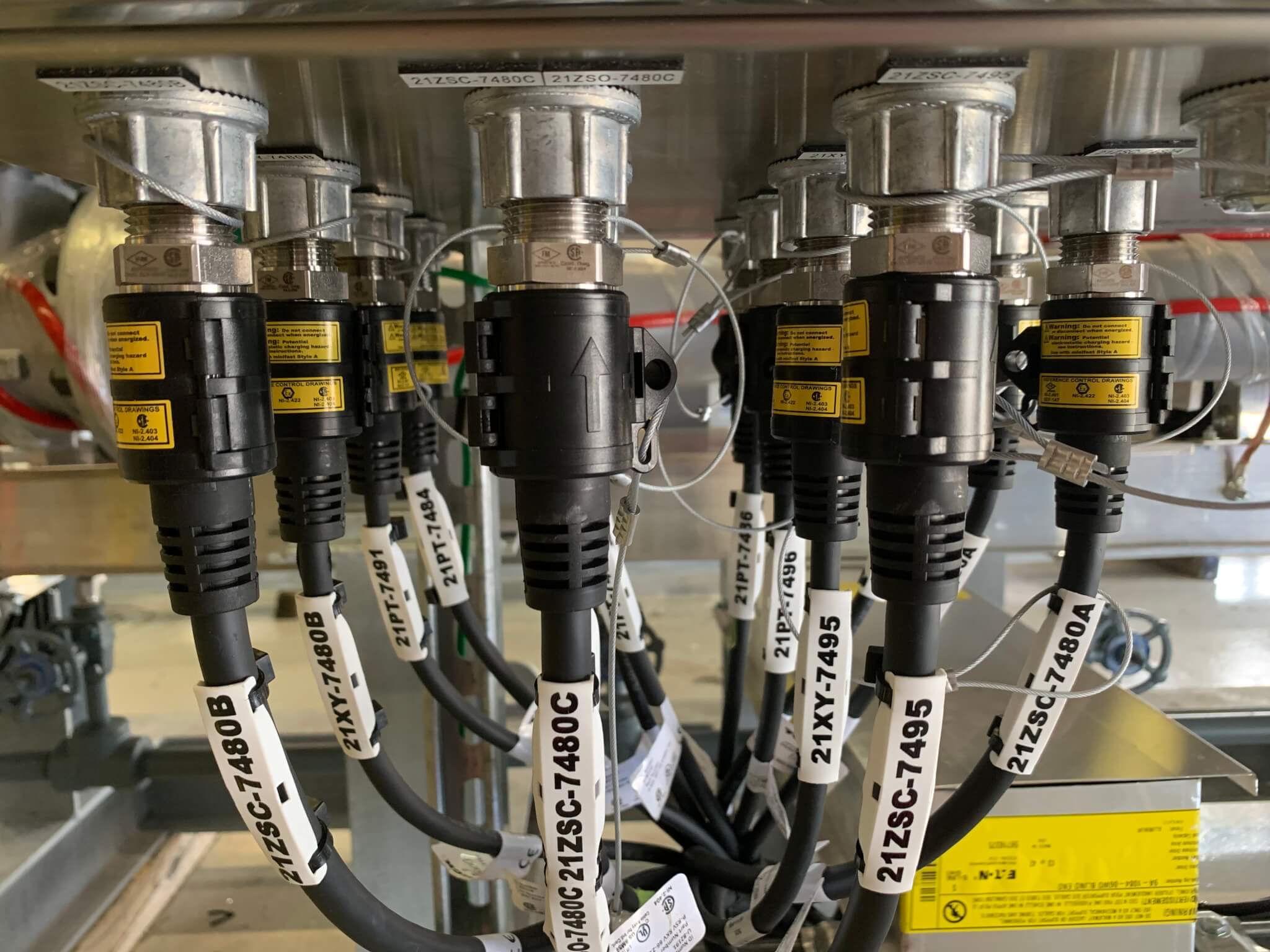
Hazardous Class 1, Division 2 Location Wiring Solution
Customer Challenge
Our customer is building a process automation (Fuel Gas and Pilot Control) skid for their oil and gas client. Our customer typically uses conduit wires or MI Cable with glands to connect their instrumentation to the control panel on their skids. Hard wiring conduit is time consuming and costly during commissioning and installation of the skid. Additionally, when a device fails or is damaged, hard wired instrumentation devices lead to longer downtime – which could mean thousands per hour for the end user. Our customer is looking for a solution that is less labor intensive by reducing their typical need for multiple cable runs, still Hazardous Class 1, Division 2, and has a quick disconnect for recalibration or replacement.
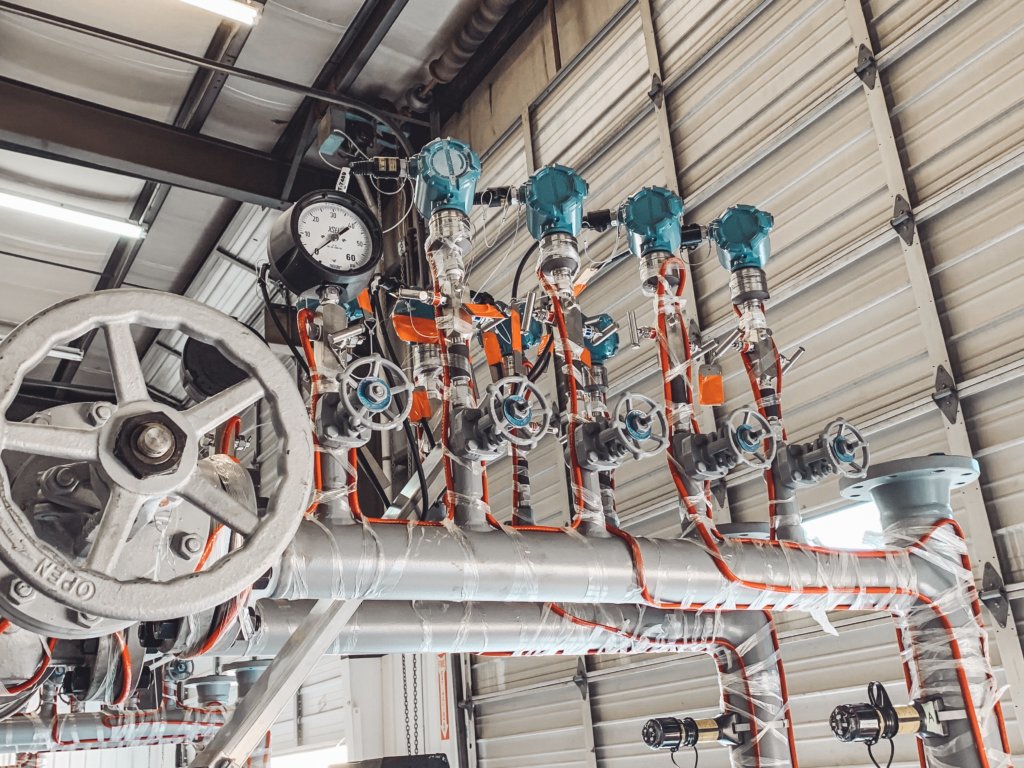
A-tech Solution
A-tech was able to solve our customer’s Hazardous Class 1, Division 2 location wiring challenge with TURCK process wiring. In this application TURCK Process Power cables and TURCK Instrumentation cables ordered in custom sizes were used with receptacles and lokfast guards. TURCK’s Quick Disconnect wiring utilizes cables terminated with preassembled or molded connectors that are used together with mating connectors and receptacles. In this application and most, cables are ordered in predetermined lengths and service loops are used to take-up any slack in surplus lengths. Receptacles were used in conjunction with a mating cordset to breach control cabinets and distribution bulkheads. The lokfast guards enable safe quick-disconnect technology in Class 1, Division 2 hazardous locations. Lokfast eliminates access to the coupling nut making disconnection impossible, warns the user to disconnect power before removing and requires a tool for removal.
Customer Benefit
Installation time required for a single cable with molded connectors is significantly less than hard-wiring the same device—in fact it is three to five times less. It is much quicker to thread a connector onto a mating connector and dress the cable when compared to bending conduit, cutting it to fit, installing it, pulling wires and finally making connections to terminals. TURCK cables are an all-in-one solution that saved our customer substantial material and labor costs by eliminating the need for any conduit to be ran from the Instrumentation device to the Control Panel.
Another huge benefit of TURCK process wiring for the end user is the maintenance savings- the lokfast quick-disconnect allows for the end user to quickly unscrew the connector if the instrumentation needs to be replaced or recalibrated. With the previous method of hard wiring with conduit, this disconnect would be far from quick and require extensive on-site labor.
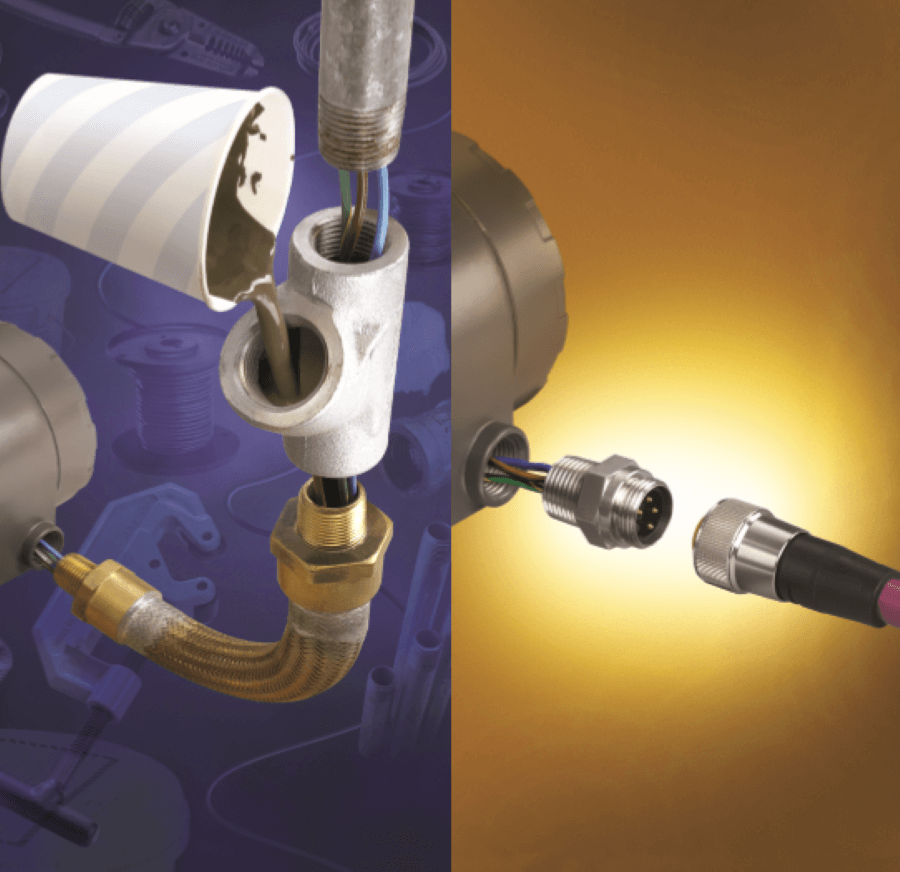
An additional highly important safety advantage of TURCK process wiring is that the receptacle and molded cordset acts as a gas block and does not require a “chico” seal. Hard-wiring leaves the potential for installers to forget to add the seal and no one knows until something catastrophic happens. With TURCK there is no “forgetting” as it is inherently sealed.
Lastly, our customer ships skids all over the US and TURCK process wiring allowed them to have the transmitter and control panel pre-wired before shipping. Once the skid arrives to its destination it can just be plugged in with double ended TURCK cordset and it is operational!
At A-tech we have a high level of technical expertise that sets us apart from our competitors. We will find the application that is best for our customers automation needs and budget. Call A-tech @800.225.6102