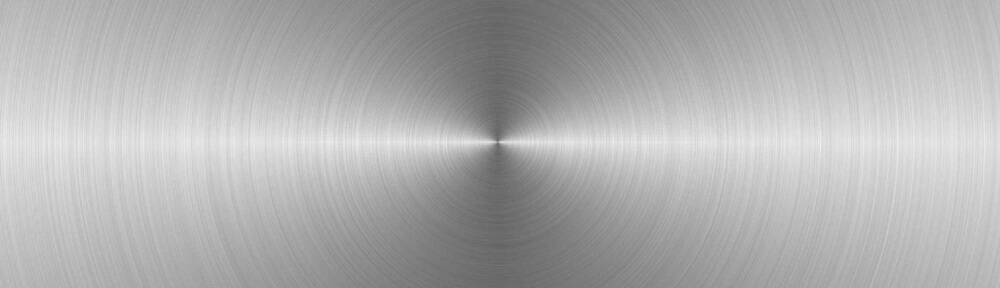
Guide to Mounting Sensors: When to use Flush and Non-Flush Mounting
Inductive Proximity Sensors
Inductive proximity sensors are the automation worlds proven solution for safe, non-contact detection of metal objects. An inductive proximity sensor can detect metal targets approaching the sensor, without physical contact with the target. This type of technology detects the presence or absence of ferrous objects using electromagnetic fields. Their applications include detection, position, inspection, and counting in automated machines, robotics, and consumer products. Manufacturers typically select which inductive sensor to use in their application based on their form factor and switching distance.
An important decision in inductive sensor selection is type of mount that will be needed to optimize performance. Improper mounting conditions can cause the sensor to false trigger, decreasing its reliability and efficiency. There are several mounting options available for this type of sensor, including non-flush mount and flush mount. Learning more about each type will help you choose the best inductive sensor for your application. Below we will get into the specifics of non-flush and flush mounts and when it would make sense to use each type of sensor.
Non-Flush Mount
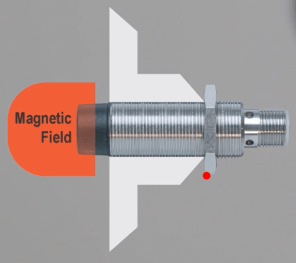
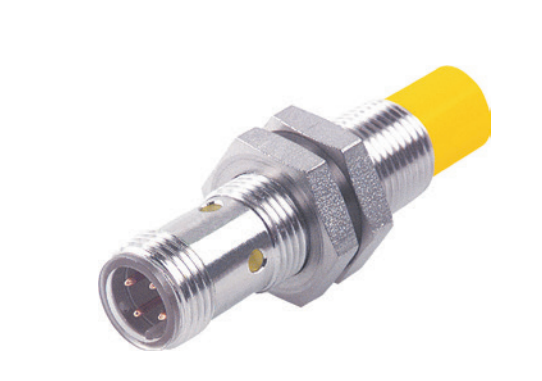
These sensors have no provisions for shielding the electromagnetic fields used for sensing. Therefore they require the largest metal-free area around the sensing head. They may also need additional mounting distance from nearby sensors to avoid mutual interference. Non-flush typically have the longest sensing distance of the three types. A non-flush inductive proximity sensor can be identified by the fact that it extends out the farthest from the mounting bracket and has a colored cap that surrounds the sensor face. Since it sticks out the farthest this type of sensor can be more likely to experience damage or be bumped, which can lead to failures for the sensor.
Flush Mount
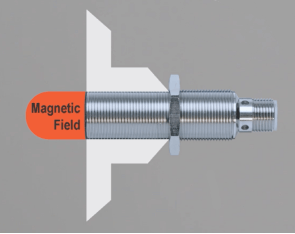
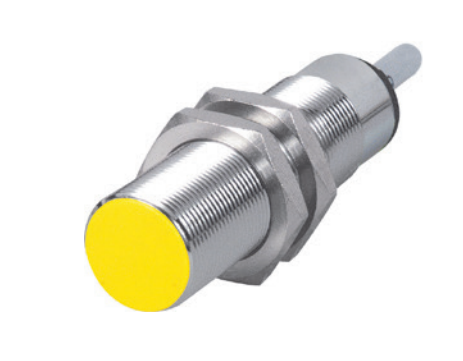
These sensors are completely shielded from all sides, except the sensing face. They are flush with the mounting surface. The sensing distance is restricted, but these sensors offer the most flexible mounting options and least interference from nearby sensors. A flush mounted sensors design causes the magnetic field to only generate out of the face of the sensor. This allows the sensor to work properly by avoiding triggering from the mount as opposed to the target. The disadvantage of flush mounts is that it creates shorter switching distances than other mounting types.
Analyze the Pro and Cons
Non-flush sensors have the advantage of a larger sensing range because they need no shielding towards the exterior, so the sensing field can extend without restriction. However, many sensor purchasers still tend to buy flush devices because these can be fully recessed into the surrounding material, making them significantly less susceptible to accumulated dirt or mechanical damage. Keep these factors in mind when purchasing inductive proximity sensors.
To discuss how Inductive Proximity Sensors can help your company, contact us at (800) 225-6102 or sales@atech-inc.com